BLOG #4: The Final Design
- alexabm0123
- Nov 25, 2023
- 3 min read
The tasks that have been completed to this point have been Tasks 4-8 ; Task 4 which is the completion of our 3D CAD Design, Task 5 which are the calculations needed to justify our final design, Task 6 being the discussion on practicality, Task 7 Finalizing our idea, and Task 8 which is optimizing using our final design using COMSOL.
As of now we have had a total of three different designs that we know could work but finalized our final design by prioritizing safety and comfortability of the device. We want our device to be easy to use for any skier but also be safe to use and will save any skier from falling.
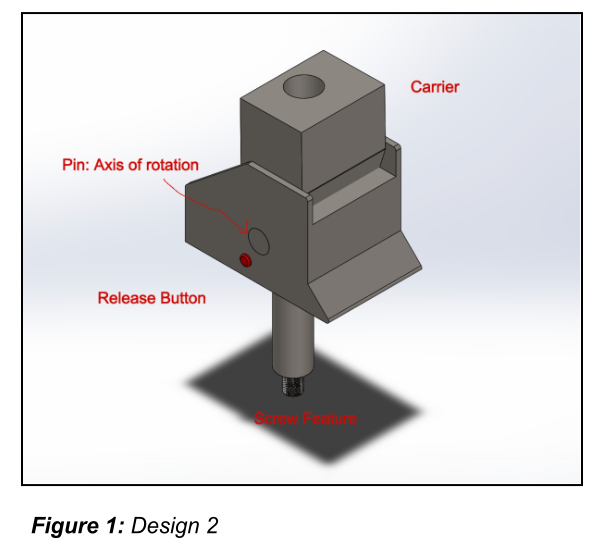
In figure 1 and 2 we see the two initial designs that we came up with as a team. As we can see figure 1 is very inconvenient since we see that the button of the design is very inconvenient for a skier since they can easily press the button which will deploy to an ax and will defeat the purpose of our ski pole.

In figure 2 we see the initial 2D drawing and the CAD drawing which shows the button below where the skier holds the ski pole. Although this idea could be safe since it is far from reach from the distance of a finger, which means when an accident occurs and the skier wants to use our device as an ax it will take longer to deploy the ax and will defeat the purpose of our device.
We finally see the final design in figure 3 which shows our deploy system that we believe will be the safest as well as the most convenient. Our primary design utilizes a pivot piece that rotates inside a harness, with notches to fit our springs in places. There is also a lockpin that is responsible for locking the position of the pivot piece. This locking mechanism only allows the pivot piece to move freely when the button end is pushed down, similar to how a key unlocks a door.
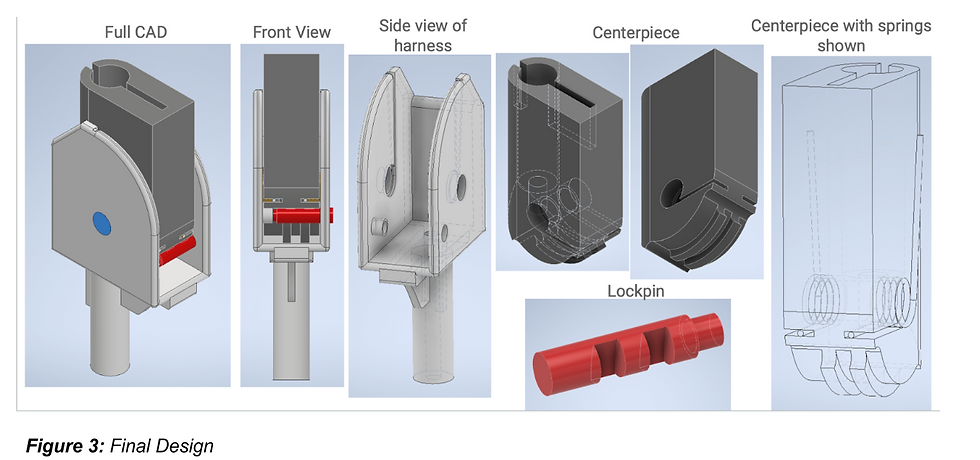
As part of our task, we conducted spring calculations to determine the most suitable spring for our device, ensuring it can effectively deploy the axe. These calculations have guided us in identifying the precise springs required for Capstone 2. Which led us to the springs down below.

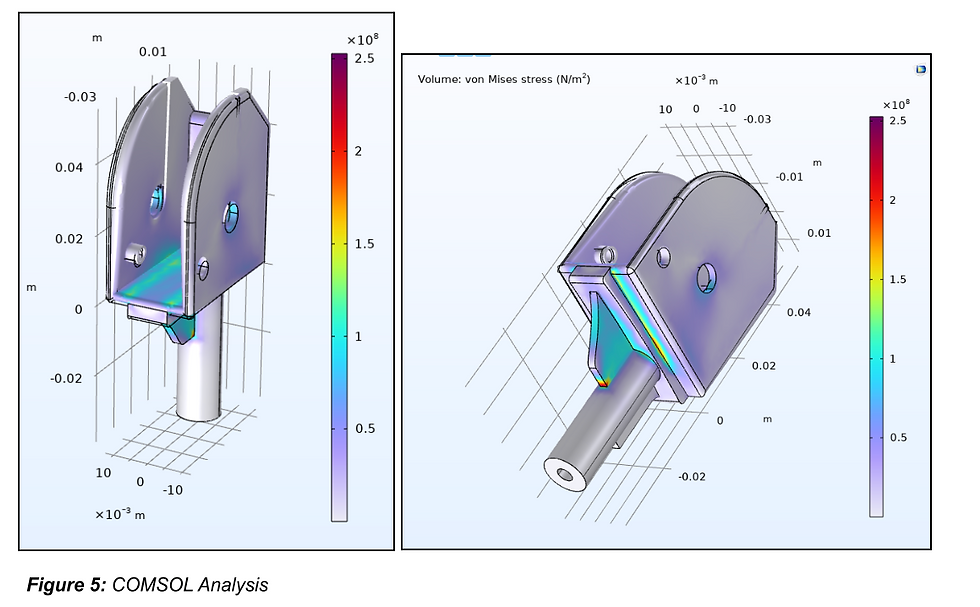
The Comsol analysis has given us maximum strain magnitudes on the order of 10^8, which is approaching the yield strength of aluminum. However, these maximum strains occur in regions of the geometry that are very sharp and unoptimized. We believe with some redesign, we can achieve a greater factor of safety.
Over the Thanksgiving break, our team diligently prepared and practiced talking points for the upcoming final design presentation. We are confident in effectively communicating the project's main design features and specifications. Additionally, we concentrated on finalizing the design for integration into COMSOL Multiphysics for FEA analysis after productive brainstorming sessions. In preparation for the final report, the team is adding sections as per instructions. We eagerly await the graded progress report to identify and correct any errors in the previous document. We have also started purchasing essential parts that we will need for Capstone since we know some things may take time to ship.
Going into Capstone 2, our team will need to focus on creating physical prototypes, and reiterating our device design. Our main approach will be 3D printing our mechanism, testing it, and then revising our design.
Comments