BLOG #8: LET'S VALIDATE
- alexabm0123
- Apr 11, 2024
- 5 min read
FINAL MANUFACTURED PRODUCT
During this period, we've achieved a significant milestone by finalizing our product and initiating the validation stage. The completion of Milestone 4 marks a pivotal moment for us. Currently, we're focusing on Milestone 5, which involves validating the final solution.
The manufacturing process for the connector and chassis proved to be time-consuming, particularly in bringing the 3D-printed parts to steel. Regarding the carrier, our intention is to utilize carbon fiber PLA due to its superior strength and ability to withstand applied forces. However, due to resource constraints within the ASME Lounge, we proceeded with the validation using regular PLA filament.
Fortunately, the ASME Lounge has now arranged for the manufacturing of our carrier using carbon fiber, and we will begin validation with the new prototype constructed from this material.
VALIDATION and RESULTS
We conducted 7 validation tests:
Deployment Time
· Measurement of Max Force
· Measurement of Weight
· Failure Rate
· Cold Temperature Operation
· Ergonomics
· Strain Gauge
Overall, we are pleased with the outcome of our validation process, as it met our expectations in many aspects. However, there were a few tests that did not yield the desired results, such as the Maximum Force measurement for Test B and the failure rate test.
The failure of the Maximum Force test can be attributed to the carrier being made of regular PLA filament, which was not our intended material. We plan to conduct this test again once the carrier constructed from carbon fiber is completed.
Regarding the failure rate test, the shortcomings were primarily due to design issues that can be rectified.
In summary, while there were some setbacks, we remain optimistic about addressing these challenges and refining our product further.
Deployment Time
Objective:
To validate and measure the deployment time of the foldable ice axe, ensuring it meets the target value of less than 1 second.
Pass, Less than .2 seconds. Need to measure time using video framerate for exact answer.
Measurement of Maximum Force
Objective:
To validate and measure the maximum force exerted on the foldable ice axe, ensuring it meets the target value of 1000 Newtons (N).
Reference: Type-1 ice tool heads are tested to 1000-N at 100-mm in XX direction and 600-N at 500-mm in YY direction (diagrams below). Testing in both directions could be a good way to make sure Carrier and Base components can withstand the moments needed during a self-arrest, even if you use lower forces than a piolet.
150kg is a heavy estimate. We usually used 1-kN as rough estimate of a human with a pack, unless alpine skiing has a higher average participant weight than ski-mountaineering. We found a heavy male could apply maximum of 3-kN with an intentionally harsh bounce on an ice-tool.
TEST A
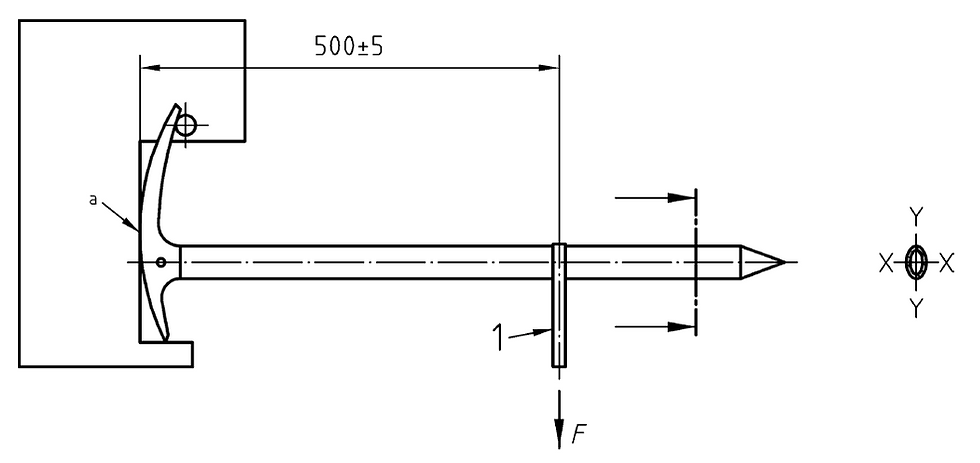
TEST B

RESULTS:
Test A:
Withstood 100 kg of weight at force point. Passed test
Test B:
Withstood 50 kg of weight at force point. Failed 60 kg. Failed test
Measurement of Weight
Objective:
To validate and measure the weight of the foldable ice axe, ensuring it meets the target value of less than 500 grams (g).
Test Cases:
Weighing Scale Measurement:
Place the foldable ice axe on the weighing scale and record the measured weight.
Repeat the measurement multiple times to verify accuracy and consistency.
Ensure that each measurement falls within the target value of less than 500g.
Pass, weight of deployment device 469g, total weight 914g
Failure Rate Measurement
Objective:
Must withstand 500 openings without failure.
Deployment Testing:
Perform 500 deployment tests.
Record any failures during deployment.
13 fails in 500 Failed Test

Cold Temperature Operation
Objective:
Validate the operation of the foldable ice axe within the temperature range of -5 ± 15 degrees Celsius.
Temperature Variation Testing:
Test the ice axe operation at -20°C, -10°C, and 0°C to simulate different cold conditions.
Ensure the ice axe functions properly within the specified temperature range.
Validation Procedures:
Place the foldable ice axe in a cold chamber set to -5 ± 15 degrees Celsius.
Operate the ice axe according to standard procedures.
Monitor its performance and functionality under cold conditions.
Repeat tests at different temperature points within the specified range.
Operated at 8 degrees F without failure. No opening failure in 50 tests. Pass
Ergonomics, Grip, and Usability Validation with Ski Gloves
Objective:
Validate the ergonomics, grip, and usability of the foldable ice axe when used with ski gloves through user surveys.
User Survey:
Distribute surveys to users who have tested the foldable ice axe while wearing ski gloves.
Gather feedback on ergonomics, grip comfort, and usability aspects.
Survey Questions:
Rate the ergonomics of the ice axe handle when used with ski gloves on a scale of 1 to 5.
Provide feedback on grip comfort and usability with ski gloves.
Include open-ended questions for additional comments or suggestions.
Validation Procedures:
Design a user survey focusing on ergonomics, grip, and usability aspects specifically related to using the ice axe with ski gloves.
Distribute the survey to a sample of users who have tested the ice axe with ski gloves.
Collect and analyze survey responses to identify trends and areas for improvement.
Survey answers
Pass

Strain Test
Our team measured strain in two places: On the side of the chassis, and on the contact surface between the lockpin and carrier. The values we obtained are reasonable and confirm our findings from computer aided FEA.
Rather than loading the device perpendicular to the ski pole like in the “Measurement of Maximum Force” test, this time, the force was applied in the same direction of the length of a ski pole. This is to say, we applied axial tension.
“Strain 1” is from the gauge on the side of the chassis, and “Strain 2” is from the gauge against the lockpin.
The results follow our expectations; the strain gauge on the chassis experienced less strain than the gauge on the lockpin. This is because the lockpin directly carries part of the load, so there is more stress. Meanwhile the gauge on the chassis would only experience stress due to indirect deformation. The metal is also much stiffer than the plastic, so less strain would be expected in the first place.
We are not entirely confident about how to interpret this data, since the materials we conducted this test under are not the same materials that we analyzed under computer-aided FEA. Still, the data follows what we would generally expect from this kind of test. Further tests are required before we can definitively say if our computer models are correct.
UPCOMING TEST
We will redo the measurement of maximum force and strain test with the carbon fiber to test how much stronger our device will be. We also plan to conduct additional strain tests in various scenarios, recognizing that a fall can occur in diverse situations. The strain gauge test will be more conclusive once the final materials are implemented, and we will be able to compare theoretical values against reality. However, the strain gauge on the chassis was broken after testing.
Our team is looking to acquire more gauges, or resort to being creative with how we conduct future testing. Although we live in Houston, where mountains for skiing are not available, we have devised an alternative plan. We intend to utilize a hill with mud to simulate a ski fall, providing us with an opportunity to test our device in real-world scenarios.
Comments