Blog #7: It WORKS!
- alexabm0123
- Mar 23, 2024
- 4 min read
WORK COMPLETED
We have successfully developed our first working prototype using infused PLA. This milestone represents a significant achievement for our team, as it confirms the functionality of our device and its ability to deploy effectively. Currently, we are focused on machining the final prototype to enhance its strength and ensure it can withstand the forces it will encounter.
We are currently working on the machining process of our device which consist of three main components: Machining the Chassis, 3D printing the carrier, and assemble.
Machining the Chassis
Currently, we are in the process of machining the chassis, which is the most time-consuming aspect of our project. Based on our Finite Element Analysis (FEA), we determined that Stainless Steel is the most suitable material for the chassis to ensure its durability. This task is being handled by our skilled welder and machinist, Juan Rodriguez.
We provided Juan with a detailed 2D blueprint of the chassis, which includes various measurements for his reference. This blueprint serves as a guide for machining the chassis accurately according to our specifications.
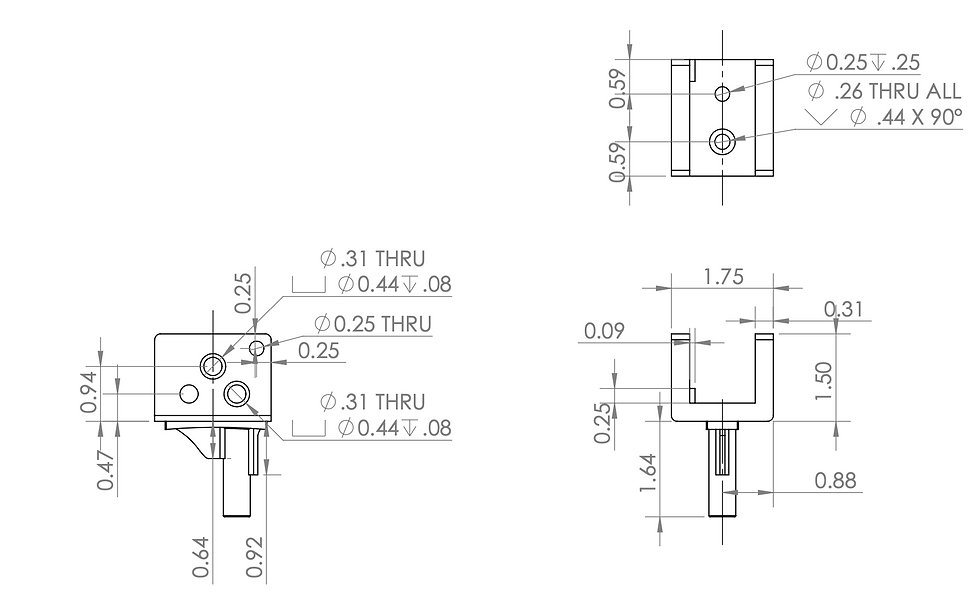
So far, the progress of our Chassis is shown below. As you can see is about 80% done where the holes are drilled, they still need the counter boles and one counter sunk at the bottom so when the bolts are added they will lay flat on the chassis and will not stick out.
3D Printing the Carrier
We have successfully 3D printed the carrier using infused PLA. To enhance its strength and durability to withstand the forces it will encounter, we are in the process of confirming with ASME 3D printing services to print the carrier using carbon fiber PLA. We have discussed with Kevin Attieh, the ASME Lounge manager and he would let us know when the material is ready, but ensures us that we will have enough time to validate our final prototype. This material offers superior strength properties, ensuring that our carrier meets the required standards for our project.
Assemble
As of now, we have assembled a 3D printed version of our device with the springs and bolts that we plan to use for our final prototype. The design of our device is finished. All further steps from here will be to recreate our 3D printed version out of more desirable materials. The smaller components of our device, - like the lever to the locking mechanism and miscellaneous pins, - are relatively straightforward to obtain, or are already in our possession. The biggest steps we have left in our device assembly is the 3D printing of the carrier out of carbon fiber, and the machining of the of the Chassis. Our team is already in the process of completing these steps, but as of writing, they are still in progress.
TEAMS PLAN
During the upcoming work period from March 24 to April 6, our team has outlined several key objectives and milestones. These include completing the machining process of the chassis and receiving it from the machinist, ensuring the high-quality 3D printing of the carrier with final infill. Additionally, we will present the current prototype to Dr. Agrawal on our demo day and work on our final validation plan.
After those tasks are done, will be begin setting up our validation procedure. We will be validating the strength of our device by stress-testing it with weight and measuring the load with a force meter. Our team is working to borrow a force meter from the UH engineering department to achieve this. We will be validating the reliability of our device by deploying it in different scenarios, - under freezing conditions, in different orientations, and against physical obstruction. Ergonomic validation will be conducted primarily by gathering user feedback, but also throughout the other validation processes. Moreover, we plan to commence work on the final build and initiate preparations for the final presentation. These tasks collectively form our near-term agenda, aiming to advance our project towards its ultimate goals efficiently.
OBSTACLES
As we anticipate the project work over the next two weeks, several potential obstacles have been identified. One challenge involves shipping times for additional hardware, which could delay progress. To mitigate this, our team plans to order additional hardware well in advance or invest in expedited shipping options to ensure timely delivery. Another obstacle could arise if we require different hardware sizes than initially anticipated. To address this, we intend to order additional sizes of hardware earlier and maintain a stock of various sizes on hand. Additionally, finding sufficient time for prototype validation poses a potential hurdle. To overcome this, we will proactively plan validation days in advance to ensure efficient testing of our device. Lastly, securing users to test the device could prove challenging. In response, we will compile a list of individuals within our network who ski and can readily meet with us to test the device firsthand, thereby facilitating the user feedback process. These solutions and backup plans are intended to preemptively address potential hurdles and maintain the project's momentum effectively.
Comments